Different Types of Backup Rings Compared for Various Applications
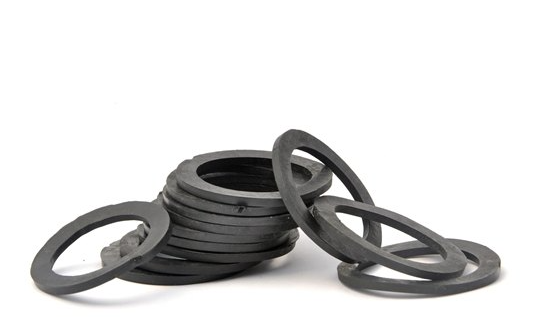
Backup rings play a role in sealing systems by preventing leaks and maintaining the integrity of fluid or gas sealing applications. They provide support to the sealing component, like O rings or seals. Help prevent extrusion or spiral failure under high pressure or dynamic conditions. When selecting a ring, factors such as the type of fluid or gas being sealed, pressure and temperature conditions, speed and frequency of motion and presence of corrosive media must be considered. Here is reference for the types of backup rings and their suitability for applications.
Polymer backup rings are widely used in sealing systems due to their resistance to wear chemicals and high temperatures. They are typically manufactured using materials like polytetrafluoroethylene (PTFE) or thermoplastic elastomers (TPE). PTFE backup rings offer chemical resistance and low friction properties that make them suitable for sealing applications involving media. Furthermore they have a temperature range covering both temperatures and high heat environments. On the other hand TPE backup rings provide flexibility and resistance to compression set making them well suited for dynamic sealing applications.
Metal backup rings are commonly utilized in sealing applications that involve pressure and temperature where polymer backup rings might not be appropriate. These backup rings are typically crafted from materials, like steel or brass known for their strength and durability. By providing support to the sealing component, metal backup rings prevent extrusion and maintain the integrity of the seal even under extreme operating conditions.
Spring loaded backup rings on the hand incorporate a spring mechanism to offer support and compensate for any potential wear or deformation of the seal over time. They find their application in sealing scenarios where frequent motion or pressure fluctuations occur. The design with a spring mechanism ensures pressure on the seal guaranteeing a seal and preventing any leakage.
In situations where standard backup rings are inadequate for sealing requirements, custom backup rings come into play. These bespoke backup rings can be. Manufactured based on the specifications of the application at hand. The material composition of custom backup rings can vary widely depending on application demands, including options such as polymers, metals or even a combination of both materials.
Conclusion
Backup rings are components in sealing systems as they provide support and prevent the primary sealing element from experiencing extrusion or spiral failure. The choice of backup ring material and design depends on application requirements such as the type of fluid or gas pressure and temperature conditions, speed and frequency of motion and the presence of any corrosive substances. Polymer backup rings are known for their resistance to wear, chemicals and high temperatures while metal backup rings are suitable for applications involving pressure and high temperature. Spring loaded backup rings offer support and compensation, for seal wear or deformation while custom backup rings can be tailored specifically to meet the needs of a sealing application. By selecting the backup ring engineers can ensure that sealing systems perform reliably and effectively in a wide range of applications.