From CAD to Reality: A Journey into the World of Rapid Manufacturing
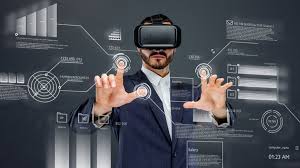
In the dynamic realm of modern manufacturing, the transition from Computer-Aided Design (CAD) to tangible reality has undergone a revolutionary transformation with the advent of Rapid Manufacturing.
This article delves into the intricate journey from the digital realm to the physical, exploring the principles, technologies, and impact of Rapid Manufacturing on various industries.
Rapid Manufacturing, also known as advanced manufacturing or additive manufacturing, represents a paradigm shift in the production process, promising unparalleled speed and efficiency.
Understanding Rapid Manufacturing
Rapid Manufacturing is a cutting-edge approach that aims to accelerate the production process, minimizing lead times and maximizing efficiency. It encompasses a range of technologies that convert digital designs into functional prototypes or end-use products swiftly.
At its core, Rapid Manufacturing aims to bridge the gap between design and physical reality, transforming concepts into tangible products with unprecedented speed. This approach challenges traditional manufacturing methods by prioritizing flexibility, cost-effectiveness, and customization.
The Role of CAD in Rapid Manufacturing
At the heart of Rapid Manufacturing lies Computer-Aided Design (CAD), the digital blueprint that serves as the foundation for the entire process. CAD software allows designers to create intricate and precise 3D models, providing the necessary input for rapid manufacturing technologies.
The seamless integration of CAD into the manufacturing workflow not only enhances design precision but also facilitates a smoother transition from virtual concepts to physical prototypes, laying the groundwork for efficient and accurate production processes. CAD’s role is not merely a starting point but a dynamic component that influences the entire manufacturing journey.
Prototyping at the Speed of Thought
One of the key advantages of Rapid Manufacturing is its ability to produce rapid prototypes. Traditional prototyping methods could take weeks, but with the aid of advanced technologies, designers can now transform digital designs into physical prototypes within hours.
This accelerated prototyping capability not only expedites the product development cycle but also allows for more iterations, fostering creativity and innovation. From concept validation to functional testing, rapid prototyping stands as a pivotal stage in the journey from CAD to reality, shaping ideas into tangible forms at unprecedented speeds.
Additive Manufacturing: Building Layer by Layer
Central to the rapid manufacturing journey is Additive Manufacturing, commonly known as 3D printing. This technology constructs objects layer by layer, translating the virtual design into a tangible product.
The versatility of additive manufacturing allows for the creation of complex geometries that were once deemed impossible. As each layer is meticulously added, the digital blueprint takes physical shape, offering a level of intricacy and detail that traditional manufacturing methods struggle to achieve.
Additive manufacturing’s role extends beyond prototyping, influencing the entire production process by unlocking new design possibilities and reducing material waste.
Subtractive Manufacturing: Precision in Cutting
While 3D printing takes the spotlight, subtractive manufacturing processes play a crucial role in the journey from CAD to reality. Computer Numerical Control (CNC) machining, a subtractive manufacturing method, carves out intricate details from solid materials, adding precision to the final product.
This subtractive approach complements additive manufacturing, providing a hybrid solution that combines the strengths of both methods.
CNC machining’s ability to handle various materials and achieve high precision makes it an integral part of the rapid manufacturing landscape, contributing to the realization of complex and functional end-use products.
Materials Matter: Choices in Rapid Manufacturing
The materials used in rapid manufacturing are diverse, ranging from polymers and metals to ceramics. Each material possesses unique properties that cater to specific requirements, offering designers a broad palette to bring their digital creations to life.
The material selection process is a critical aspect of the journey from CAD to reality, influencing the product’s durability, functionality, and aesthetics.
Rapid manufacturing technologies continue to expand the range of compatible materials, enabling the production of items with diverse characteristics, from lightweight and flexible to durable and heat-resistant.
Realizing End-Use Products
Rapid Manufacturing transcends the realm of prototyping, venturing into the production of end-use products. The ability to swiftly manufacture functional components and products has transformed the traditional manufacturing landscape, enabling businesses to respond promptly to market demands.
This shift towards end-use production marks a significant evolution in rapid manufacturing, showcasing its capability to not only create prototypes but also contribute to the manufacturing of final, market-ready products.
This transition is reshaping supply chains, reducing inventory costs, and fostering a more agile and responsive manufacturing ecosystem.
Applications Across Industries
The impact of Rapid Manufacturing is felt across various industries. From automotive and aerospace to healthcare and consumer goods, this innovative approach is reshaping how products are conceptualized, designed, and brought to market.
In the automotive sector, rapid manufacturing accelerates the development of prototypes and custom components, streamlining the design-to-production timeline. In healthcare, it facilitates the production of personalized medical devices and implants.
The breadth of applications underscores the versatility of rapid manufacturing, demonstrating its potential to revolutionize diverse sectors by offering tailored solutions to unique challenges.
Sustainability in Speed
As industries embrace rapid manufacturing, questions arise about its environmental impact. Surprisingly, accelerated production processes can contribute to sustainability by reducing waste, energy consumption, and overall carbon footprint, presenting a compelling case for eco-friendly manufacturing practices.
The precision of rapid manufacturing technologies minimizes material wastage, and the ability to produce on-demand reduces the need for extensive warehousing.
These sustainability benefits position rapid manufacturing as not only a solution for efficiency but also as a responsible choice for environmentally conscious businesses.
Challenges and Future Outlook
Despite its transformative potential, rapid manufacturing faces challenges such as material limitations, post-processing requirements, and cost considerations. However, ongoing research and development promise to overcome these hurdles, paving the way for an even more streamlined and efficient future.
Advancements in material science aim to expand the range of materials compatible with rapid manufacturing, addressing current limitations and opening new possibilities.
As the technology matures, cost-effective solutions and optimized workflows are expected to become more prevalent, making rapid manufacturing increasingly accessible to a broader range of industries.
Conclusion
The journey from CAD to reality through Rapid Manufacturing is a testament to the convergence of digital innovation and tangible outcomes. As this technology continues to evolve, businesses and industries must adapt to the changing landscape, embracing the speed, precision, and limitless possibilities that rapid manufacturing brings to the manufacturing realm.